Understanding LOLER Compliance in South Wales: A Comprehensive Guide
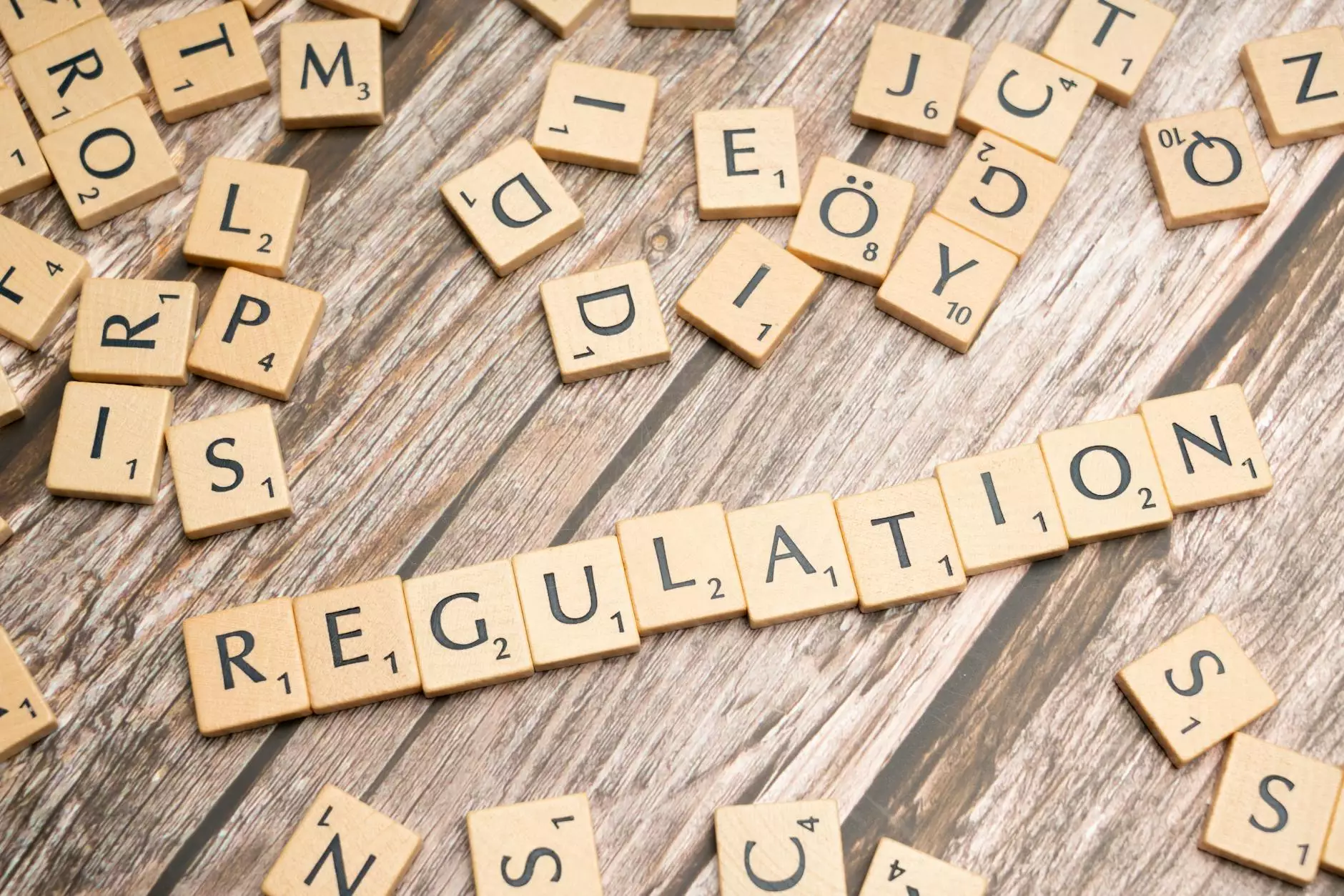
LOLER compliance is not just a regulatory requirement; it is a fundamental aspect of maintaining safety and operational integrity across various industries. In South Wales, businesses particularly in sectors like Home & Garden, Gardeners, and Pest Control must adhere to these regulations to ensure both employee and equipment safety. This article delves into what LOLER compliance entails, its importance, and how businesses can implement it effectively.
What is LOLER Compliance?
The Lifting Operations and Lifting Equipment Regulations 1998 (LOLER) are regulations that govern the safe use of lifting equipment in the UK. The key aims of these regulations include:
- Ensuring that lifting equipment is suitable for the tasks it is intended for.
- Proper inspection and maintenance of lifting equipment.
- Ensuring that operations involving lifting equipment are conducted safely and efficiently.
In South Wales, compliance with LOLER is critical, especially for businesses that rely on lifting equipment to operate effectively. These may include construction crews, maintenance teams, and even those in the gardening and pest control industries who use various forms of machinery for their daily tasks.
Why is LOLER Compliance Important?
Adhering to LOLER compliance regulations is essential for several reasons:
1. Safety of Employees
One of the primary goals of LOLER is to protect the workforce. Equipment failure can lead to serious workplace accidents, which can have devastating effects on employees. By ensuring proper compliance, businesses minimize risk and create a safer working environment.
2. Legal Obligations
Failure to comply with LOLER can result in legal repercussions, including hefty fines and liability for accidents. Businesses in South Wales must be aware of these legal obligations to avoid sanctions and maintain operational licenses.
3. Equipment Longevity
Regular inspections and maintenance not only enhance safety but also extend the lifespan of lifting equipment. By adhering to LOLER compliance, businesses can ensure that their equipment is functioning optimally and avoid costly downtimes.
4. Improved Reputation
A business known for its commitment to safety is more likely to attract customers and retain employees. LOLER compliance can significantly enhance a company's reputation in the marketplace, particularly in competitive industries.
Key Components of LOLER Compliance
To ensure compliance with LOLER, businesses must focus on several critical components:
1. Risk Assessment
Before any lifting operation, a comprehensive risk assessment should be conducted. This process helps identify potential hazards associated with lifting operations and measures to mitigate them.
2. Selection of Equipment
Choosing the right equipment for the job is paramount. Equipment must be suitable for the specific lifting task and should be marked appropriately to indicate its limits.
3. Regular Inspections
LOLER mandates that all lifting equipment be thoroughly examined at regular intervals. Inspections should be conducted by a qualified person who can assess the condition of the equipment and identify any necessary repairs.
4. Maintenance and Repairs
Maintaining lifting equipment in a safe condition is a legal obligation. Recorded and timely maintenance schedules can prevent unexpected failures and keep the equipment in top condition.
5. Training and Competence
Employees operating lifting equipment must be adequately trained and competent. Providing proper training not only adheres to LOLER but instills confidence in the workforce, leading to safer operations.
The Role of Safe Plant UK in LOLER Compliance
Safe Plant UK (found online at safeplantuk.co.uk) offers a range of services designed to assist businesses in South Wales with their LOLER compliance needs. These services include:
- Lifting Equipment Inspections: Comprehensive inspections carried out by qualified personnel to ensure all equipment meets safety standards.
- Training Programs: Tailored training sessions for staff on safe lifting practices and equipment use.
- Maintenance Services: Ongoing maintenance packages to keep lifting equipment compliant and operational.
- Consultation Services: Expert advice on implementing LOLER compliance strategies within your business operations.
Top Tips for Achieving LOLER Compliance
Achieving LOLER compliance can be straightforward if you follow these top tips:
- Stay Informed: Keep up with the latest updates and changes to LOLER regulations.
- Create a Compliance Checklist: Develop a checklist that outlines all required actions for ensuring compliance.
- Document Everything: Maintain clear records of inspections, training, and maintenance activities.
- Engage Professionals: Don’t hesitate to hire experts where necessary to ensure compliance.
- Review and Revise: Regularly review your compliance strategy to identify areas for improvement.
Conclusion
In conclusion, LOLER compliance in South Wales is a critical aspect of maintaining workplace safety and operational excellence across various sectors, including Home & Garden and Pest Control. By understanding the regulations and implementing necessary compliance measures, businesses can foster a safe and efficient work environment. Investing time and resources into LOLER compliance not only protects employees and equipment but also enhances your business's reputation.
For more information on achieving LOLER compliance, visit Safe Plant UK — your trusted partner in raising the safety standards of your business.
loler compliance south wales