Understanding Die Casting Components: A Key to Modern Manufacturing
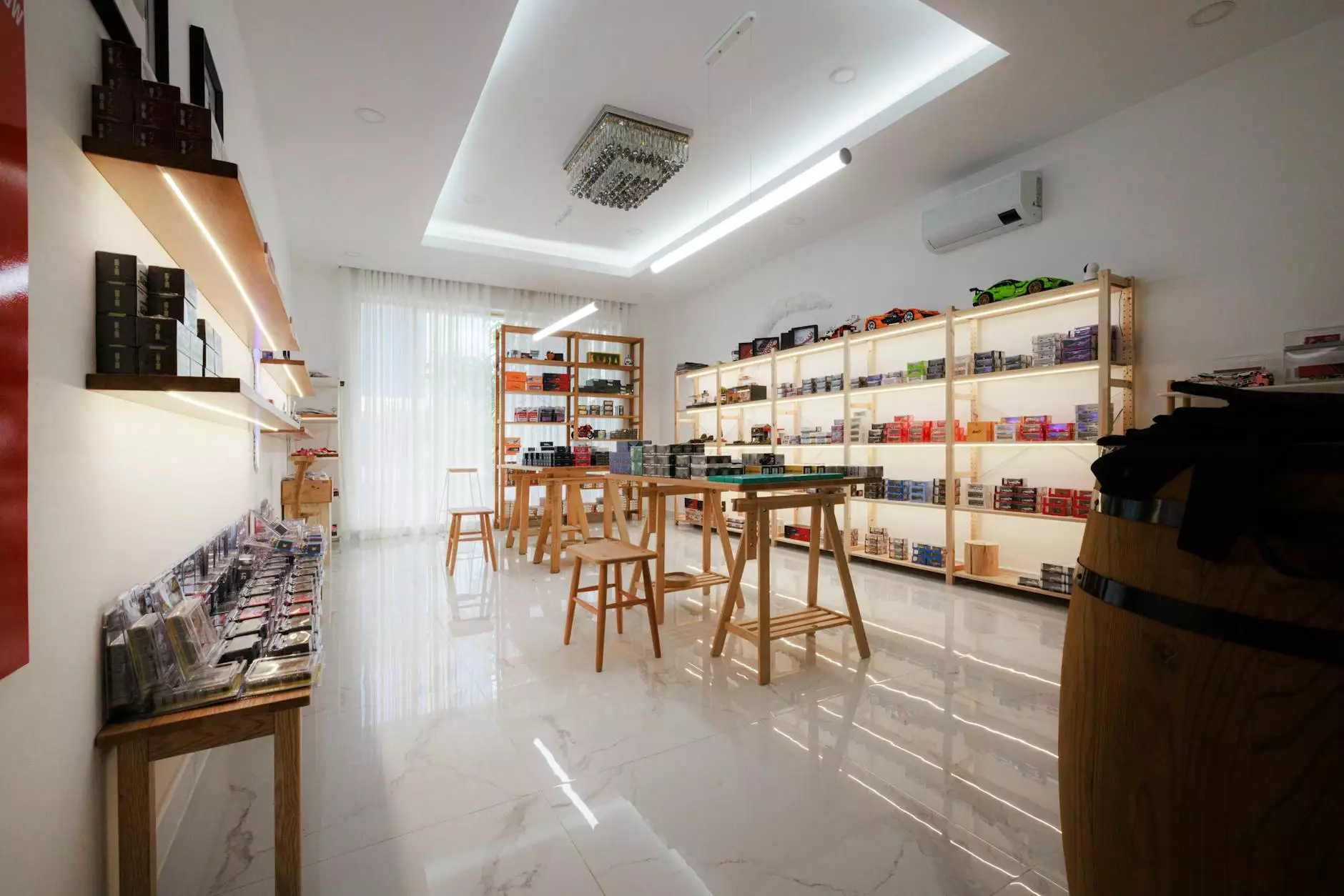
What are Die Casting Components?
Die casting components refer to parts produced through the die casting manufacturing process, which is widely recognized for creating complex shapes with high precision. This method involves forcing molten metal into a mold cavity, resulting in parts that can be used across various applications from automotive to electronics.
The Die Casting Process Explained
The die casting process involves several critical steps:
- Preparation of the Die: The mold or die is meticulously designed and constructed to ensure it can withstand high pressure and temperatures during the casting process.
- Melting the Metal: Common alloys like aluminum, zinc, and magnesium are melted in a furnace to create molten metal ready for casting.
- Injection of Metal: The molten metal is injected under high pressure into the die cavity within a fraction of a second, ensuring that it fills every intricate detail of the mold.
- Cooling and Ejection: Once the metal solidifies, it is cooled and then ejected from the die, producing a finished component.
- Finishing Processes: Final touches such as trimming, machining, and surface treatments can be applied to enhance the aesthetic and functional qualities of the component.
Advantages of Using Die Casting Components
Die casting offers numerous advantages, which make it a preferred choice in manufacturing components:
- High Precision and Accuracy: The die casting process allows manufacturers to produce parts with tight tolerances and intricate designs, which is essential in critical applications.
- Cost Efficiency: When producing large volumes, die casting becomes increasingly cost-effective, as the process minimizes material waste and reduces the need for extensive finishing.
- Excellent Surface Finish: Components produced through die casting often require minimal processing thanks to the fine surface finish achievable directly from the die.
- Versatility in Design: Die casting can accommodate a wide variety of metals and alloys, making it suitable for diverse applications across multiple industries.
- Strength and Durability: The mechanical properties of die-cast metals provide strength and resilience, which are critical in end-use applications.
Applications of Die Casting Components
Die casting components are widely used in various sectors. Here are some notable applications:
1. Automotive Industry
The automotive sector heavily relies on die casting for producing components such as:
- Engine Blocks
- Transmission Housings
- Wheel Rims
- Fuel Gauges
2. Electronics
In electronics, die casting is crucial for:
- Heat Sinks
- Chassis Covers
- Connectors
3. Aerospace
Aerospace applications require high-performance components, with die casting producing:
- Aircraft Engine Parts
- Landing Gear Components
- Structural Supports
4. Consumer Products
Many consumer products also utilize die casting, including:
- Household Appliances
- Garden Tools
- Fitness Equipment
Choosing the Right Metal Fabricator for Die Casting Components
When selecting a metal fabricator for your die casting components, it's important to consider several factors:
1. Experience and Expertise
Look for manufacturers with a proven track record and extensive experience in die casting processes. Their expertise can significantly impact the quality of the final components.
2. Quality Assurance Practices
Ensure the fabricator employs strict quality control measures. Certifications such as ISO 9001 demonstrate a commitment to quality throughout the manufacturing process.
3. Technological Capabilities
Check for advanced equipment and technologies. Modern die casting machines and associated technologies can improve efficiency and precision, leading to better outcomes.
4. Customization Options
Your selected fabricator should offer customization to meet specific design requirements. This flexibility is essential for industries that demand unique components.
5. Cost Competitiveness
Finally, evaluate the pricing structure. While the cost should not be the only deciding factor, finding a balance between quality and cost-effectiveness is crucial.
The Future of Die Casting Components
As technology evolves, die casting components will continue to play a vital role in various industries. Future trends may include:
1. Adoption of Advanced Alloys
Developments in material science could lead to the use of more advanced alloys, enhancing the properties of die cast components.
2. Increased Automation
Automation technologies are expected to improve efficiency, reduce production times, and allow for more complex geometries in die casting.
3. Sustainability Practices
With a growing emphasis on sustainability, die casting manufacturers will likely adopt practices that reduce waste and energy consumption, positioning themselves as environmentally responsible.
Conclusion
In summary, die casting components are indispensable in modern manufacturing, offering unparalleled benefits such as precision, cost-efficiency, and versatility. By understanding the die casting process and its applications, businesses can make informed decisions about their manufacturing needs.
For businesses seeking a reliable partner in metal fabrication, DeepMould.net specializes in providing high-quality die casting solutions tailored to various industry demands.